T
he
Material Testing
Laboratory at TARAgram Datia is one of the pilot initiatives of
Technology and Action for Rural Advancement (TARA) to establish a state
of the art facility in Central India. It is engaged in research of all
kinds of waste generated by various industries such as fly ash, boiler
ash, marble sludge etc. It commenced its operations under the flagship
of TARA Environment Monitoring Facilities on the 18th of April, 2000.
The laboratory is situated on the Gwalior- Jhansi National Highway at
the 67th km milestone near Datia, Madhya Pradesh.
It is the one and only Research
and Development (R&D) Centre in India addressing and servicing the
exclusive needs of the Indian Brick Industry.
The Centre is managed by a team
of qualified professionals. A ceramic engineer is in charge of all
material testing supported by a team of BSc chemistry degree holders.
Another qualified material technologist with experience in product
development, materials testing and production research looks after the
brick sector of the R&D process. The entire R&D team is led by the
Programme Director, Dr. Soumen Maity.
Infrastructure facilities available at the
Material Testing Lab:
• Testing facilities for soil,
green and fired bricks and fuel ash.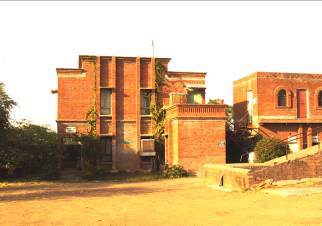
• Demonstration of improved
methods for soil storage and handling, mix preparation, firing and
performance monitoring.
• Balanced mechanisation to
ensure easy handling of green bricks at each and every step of the
production process.
• Production facilities for
demonstrating state of the art systems and resultant high quality green
bricks, fired bricks, fuel ash bricks (cured block) and other specialty
products like potteries, designer bricks, tiles etc.
• Skilled manpower in terms of
R&D, problem analysis, consultancy services, state of the art firing and
fly ash brick production.
• Training facilities for
masons, moulders, extruder operators and fire masters.
Other facilities available are as follows:
a. Hardware: Four shaft VSBK,
extruder system, semi mechanised green brick making, pug mill, brick
lifting system, metallic R&D shaft, fly ash brick making production
yard, drying sheds and handling equipment, brick bank, materials testing
laboratory with soil, fuel ash and fuel testing facilities.
b. Software: All programmes
relevant to scientific documentation and DTP.
c. Support facilities:
• Training hall
• High temperature programmable
Nabertherm furnace
• Electrical drier
• Bomb calorimeter
• Compression testing machine
• Environmental monitoring
equipment
• Temperature sensors and
scanners
• Infra-red temperature
measurement devices
• All types of soil and fuel
ash testing equipment
Ever since it started
functioning, it has innovated some excellent technologies and processes:
• Technology for industrial
waste utilisation (5% to 70%) in brick making with varied soils.
•
Technology for utilisation of stone dust (upto 40%) in brick making.
• Technology for producing hollow bricks (upto 14%).
• Technology for coal ash utilisation in brick making.
• Technology for making bricks with black cotton soil.
• Technology for making bricks with non plastic sandy soils.
• Process for ensuring the brick production unit as a "no waste
producing" unit.
• Low cost soil mixing techniques and equipments
• Low cost extruders bricks.
• Optimisation of drying time and fire schedule for various brick types
• Low cost building material technologies and processes
• Kits for field testing of soil and fly ash to determine suitability
for brick making
• Kits for field testing of coal for brick production
• Repository of over 1000 soil and fuel reference samples from the
entire country and also from South Asia and Africa
• Technology for utilisation of slag waste in pavers production
• Fly ash brick technology package
• Technology for utilisation of pond ash in cured block making
• Technology for utilisation of fly ash in Micro Concrete Roofing (MCR)
tiles production
• Technology for utilisation of black ash in cured block making
• Technology for utilisation of marble sludge in brick making with
various soils and also in cured products. q
Sarthak Kulia
skulia@devalt.org