Foundry Waste Utilisation
for
Achieving Resource Efficiency
“One man`s waste is another man`s treasure.”
Aggregates play a key role in the strength, resilience and other
physical properties of concrete structures. The consumption of
aggregates creates a huge demand for virgin resources from quarry
mining. Due to rising requirement of materials in the construction
sector, resource depletion has resulted in numerous social and
environmental issues. As a result, the ecological chain has experienced
many abrupt shocks as an environmental cost of development.
Cost effective sustainable solutions always have a huge demand in the
industry. The Development Alternatives group has developed alternative
technology to use foundry slag in paver block manufacturing by replacing
100 percent of the natural aggregates by crushed slag. This meets the
twin demands of resource efficiency and waste utilisation. This crushed
foundry slag is an ideal candidate for the replacement of natural
aggregates due to its intrinsic properties similar to natural aggregate.
The utilisation of this waste provides an additional profit to the
entrepreneur at the rate of 40 paisa per block.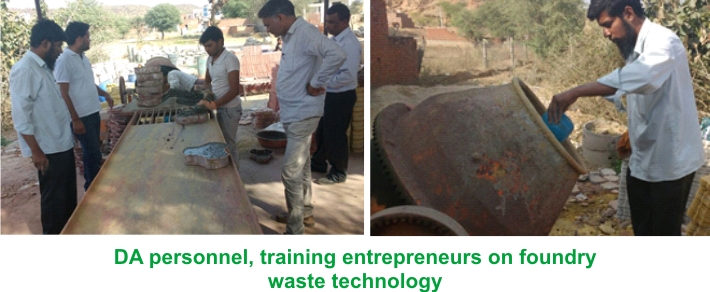
The foundry slag utilisation technology has led to benefits in two
industrial sectors. The first being the foundry owners who get a
solution for the disposal of their foundry waste and the second are the
paver block manufacturers who can avail quality aggregates` replacement
free of cost due to slag`s classification as waste.
India`s foundry sector generates 10 lakh tonnes a year with the growth
rate of 1 lakh tonne per year. This amount of waste can occupy an area
of 68.75 square km space with a depth of 1 meter! Currently this slag is
disposed of simply in un-engineered landfills. Cities like Jaipur are
left stumbling without an option of landfilling as there are many other
solid waste streams far ahead in priority as compared to foundry slag.
India’s generation of slag is predicted to multiply at an exponential
rate of 10 lakh tonnes by the year 2020 which is equivalent to an area
of 125 km2 with 1 meter thickness.
Development Alternatives along with The Foundation for MSME Clusters is
currently implementing this technology resulting in the usage of 8874
tonnes of foundry slag generating an additional income of Rs 10.444
crores and saving equivalent natural resources.
The generic perception that usage of reprocessed waste materials may
affect the quality of building material leaves investors in doubt.
However, the technology developed by DA has abated their concern with
substantial scientific evidence with Indian constructions standards as
reference. Quality of the technology is widely evident by the acceptance
of the entrepreneurs. Till date, seven enterprises have adopted this
technology on foundry waste utilisation within one and half years of
intervention with many of them in line to adopt the same.
The implementation of the technology is being carried out by:
• Sensitising workshops
• Demonstration of technology in the paver block manufacturing units
The real time demonstration of the manufacturing process with foundry
slag and natural aggregates enables the entrepreneur to understand the
advantages of technology.
Punjab is one of the states which has taken significant strides in
adopting the technology where it is capitalising its foundry waste in 5
paver block manufacturing units. Currently Rajasthan and Haryana are
also following in the footsteps of Punjab by setting up foundry waste
based paver units.
The resources shortage in our country could be addressed up to a
significant margin by utilising the huge volumes of foundry slag waste
in the construction industry. The technology is resource efficient and
cost effective. The technology needs policy support and capacity
development of more entrepreneurs so that this resource efficient
technology is utilised on a large scale across India.
■
Atheeque Ahmed. K
aahmed@devalt.org
Back to Contents
|