Innovative Policies in Material Efficiency for Urban Built Environment
As
our cities grow and try to cope with increasing demands for resources and services, new models and systems are emerging to tackle issues of resource circularity and material efficiency. In its 2020 report on ‘Resource Efficiency and Climate Change – Material Efficiency Strategies for a Low-Carbon Future’, the International Resource Panel describes the vast potential of material efficiency strategies towards climate change mitigation, especially with respect to developing countries where majority of the urban growth is predicted to take place in the coming decades.
In the built environment, the report projects that material efficiency strategies can help reduce up to 60-70% of life-cycle emissions from homes in India and China by 2050, compared to a potential reduction of 35-40% in G7 countries (Figure 1). To achieve this, it is imperative for innovative policies to evolve to a multi-stakeholder perspective covering the complete supply chain of the housing industry. While most current material-related policies consider end-of-life landfill diversion as their major focus, strategies must be developed for the planning, use and design phases as well.
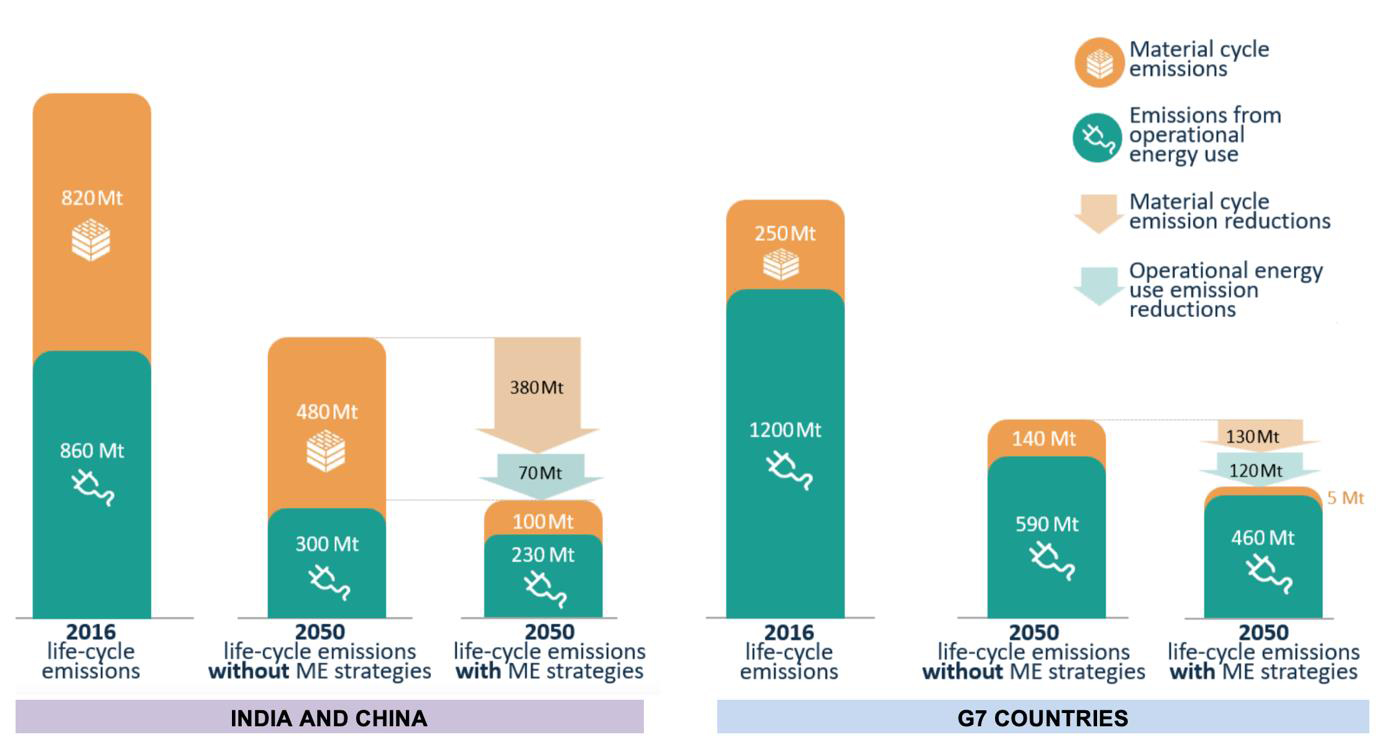
Figure 1
There Some basic strategies towards this
include material substitution in buildings along with using less
material by design wherever possible. Intensity of use of material can
also be reduced through efficient design and production using tools like
building information modelling (BIM) and space-efficient, flexible
designs using modular and prefabricated components. Additionally,
technological development is needed to enhance end-of-life recovery and
reuse potential of materials along with improving fabrication yields and
product lifetimes. From a policy perspective, strategies may include:
-
Zoning and land regulations that directly
address material usage through building codes and green certification
systems
-
Encouraging revenue departments to regulate
taxes and subsidies on virgin materials from an environmental lens
-
Facilitating new business models in housing
that benefit from enhanced performance over the life-cycle of the
building, along with innovative housing service delivery models
-
Promotion of green technologies through
public green procurement policies along with targeted marketing and
incentivisation of such materials to enhance awareness among citizens
and increase usage in private projects.
For improved city-level decision making
towards material use strategies, a comprehensive understanding of
resource requirements can be developed using tools such as Life Cycle
Assessment (LCA) and Material Flow Assessment (MFA). Under the EU-REI
project, DA has helped conduct such assessments in the construction
sector for Ahmedabad and Bhubaneswar where the housing sector is
projected to add up to 70 million sqm and 40 million sqm of built space,
respectively, between 2020 and 2030. See Figure 2 for an example of a
Sankey diagram of material flow for housing in Ahmedabad for projects
during 2014-2019 with a built up area of 32.75 million sqm.
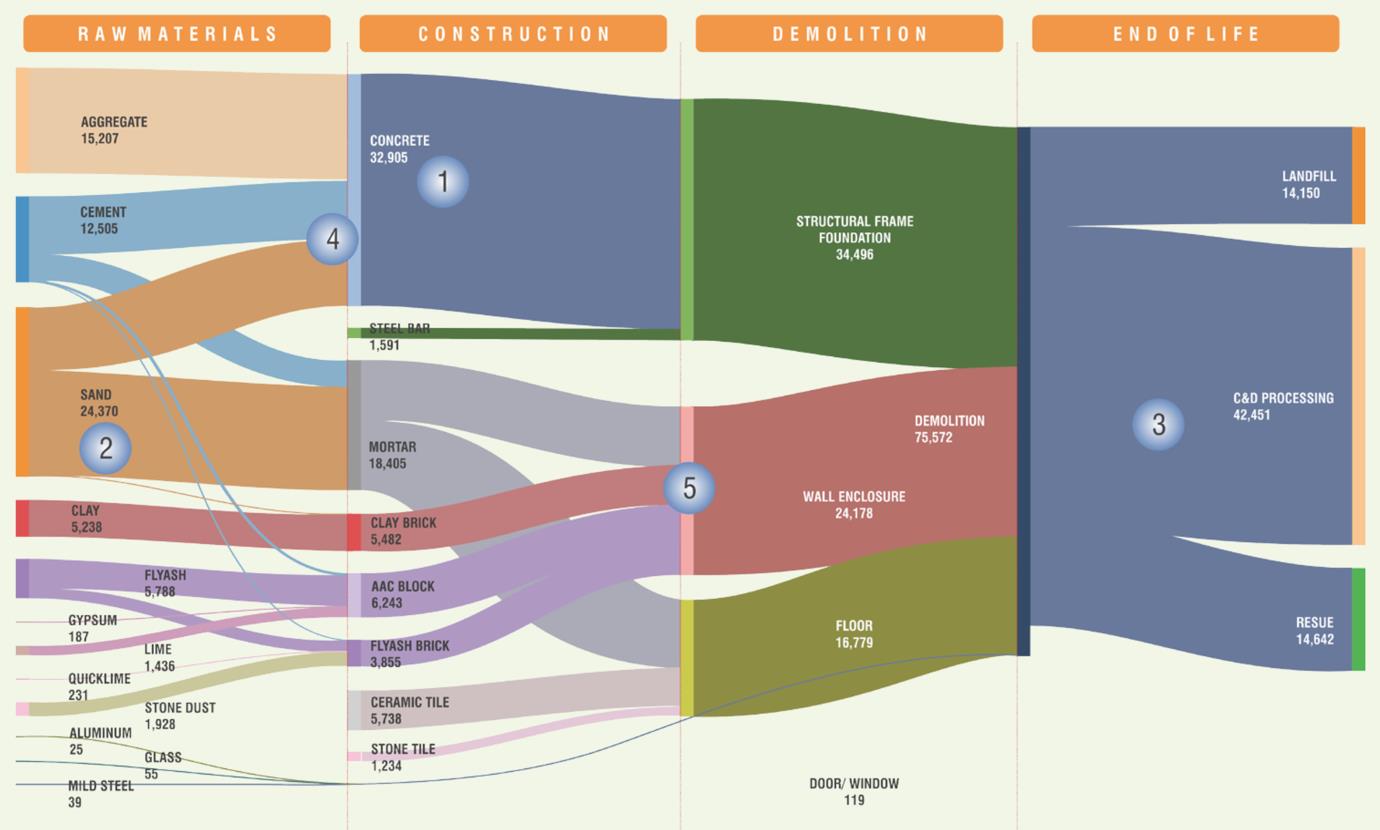
Figure 2
It was estimated that materials with a gross
weight of 2-2.5 tonnes flow to every sqm of residential built space with
an overall carbon footprint to the tune of 0.6-0.8 tonne CO2 equivalent
emissions per sqm. Concrete was found to have the highest intensity of
use, accounting for about 40% of both material weightage as well as
carbon emissions. With respect to primary material usage, highest
quantum of material flow was for sand, mostly used in concrete mixes, at
about 30-35% of total usage, while cement (50%) and steel (12%) were the
biggest contributors to emissions. Additionally, the research also
looked at the quantum of secondary resource utilisation including
construction and demolition waste, and industrial waste such as fly ash,
along with identifying priority areas for policy action. ■
Mohak Gupta
mgupta@devalt.org
Siddharth Jain
sjain@devalt.org
Back to Contents
|