Cleaner Production (CP) Scheme For Stone Crushing Industry
Safdar
Imam
safdar@sdalt.ernet.in
__________________________________________________________________________________________________________
Stone
crushing industry is an important industrial sector in the country,
engaged in producing crushed stone, used as raw material for various
construction activities, such as roads, bridges, buildings, canals etc.
The
construction and infrastructure sector was estimated to grow @ 8% per
annum in the 9th plan period.
It is estimated that, there are over 12,000 stone crushing units in
India (covering small,
medium and large scale).The number is expected to grow further in view
of the future plans for development of country infrastructure.
Stone crushing sector with an annual turnover of over Rs. 5000 crores
provides direct employment to over 500,000 people. Most of these
personnel, engaged in various activities (mining, crushing,
transportation of mined stones and crushed products etc.) are from rural
and economically backward areas, where employment opportunities
are limited.And therfore, stone crushing industry carries great
significance in terms of social importance.
The stone crushing sector,
though socio-economically important, create a substantial amount of
environmental pollution by way of both process sources and fugitive
sources.
It is a well known fact that most of the workers engaged in stone
mining, crushing, transportation etc., suffer from several occupational
health hazards (severe cough, lung disorders, etc). Dust emission has
visible adverse impact on environment. Agricultural land and forested
area are also affected due to emissions.
Keeping in view the need for worker’s health and environmental problems
associated with stone crushing sector, it become necessary and important
to develop Cleaner Production (CP) scheme to mitigate hazardous impact
on environment and human health due to regular exposure
to high dust level.
Cleaner Production (CP) as
defined by UNEP is the continuous application of an integrated
preventive environmental strategy to processes, products, and services
to increase overall efficiency, and reduced risks to humans and the
environment. Apart from pollution reduction it also provides some direct
benefits to the industry, such as:
● |
Improved operating efficiency of
the plant |
● |
Cost-
saving through reduced wastage of raw material and energy |
● |
Waste
material recovery |
● |
Better product quality and consistency |
CP
Studies in a Stone Crushing Cluster
A
study of the production process and environmental status was conducted
by Development Alternatives in four selected stone crushing units of
Madhya Pradesh with
financial assistance
from SIDBI,
Bhopal. The study was conducted through preliminary
visit & survey for collecting baseline information such as, raw
material, plant capacity, process details, equipment & energy
consumption, crushers, screens and material handling equipments etc.
In addition, dust control practices and water availability status was
also collected.
Dust Emission in a
typical Stone Crushing Unit |
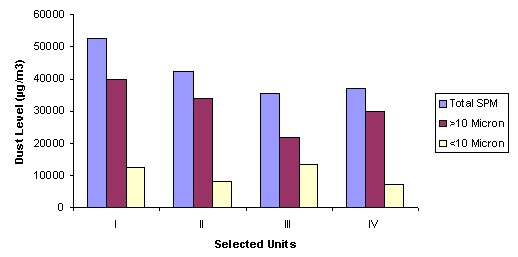 |
Based
on the results of Ambient Air Quality Monitoring (AAQM), it is found
that, the dust level in ambient air is higher than prescribed CPCB
norms(suspended particulate
matter of a stone crushing unit shall not exceed 600 µg
/m3 ). Therefore it is necessary to reduce the level of dust
in the ambient air through implementation of Cleaner Production scheme
i.e. dust suppression and dust containment. Unit level dust contribution
in typical stone crushing units is shown graphically:
In order to reduce such a
high dust level in a unit, the following cleaner production options have
been suggested:
i |
Wet type system |
ii |
Dry type systems |
iii |
A
combination of Wet and Dry Type System. |
i.
Wet
type System
This design has two
components: |
● |
Dust Containment
Enclosure Component and |
● |
Dust Suppression
System Component |
Dust Containment
Enclosures
For a wet type dust
control system to be effective, it is necessary to provide containment
enclosure for the following key locations:
● |
Enclosure for Crusher
Discharge Area |
● |
Enclosure for
Vibratory Screen |
-
Dust Suppression System
The dust suppression
system comprises of providing moisture into the material flow by
spraying water at key dust generating locations to restrain fine
particulate matter from becoming air borne. The objective of wet dust
suppression is not to fog an emission source with a fine mist to capture
and remove particulates emitted, but rather to prevent their emission by
keeping the material moist at all process stages. It is usually
necessary to apply it at several points beginning as soon as possible
after the stones are introduced into the plant. The wet type system is
useful in the place where water is easily available. The cost is less as
compared to dry type system and reduces dust upto 70% in the ambient
air.
Dry
type systems
Keeping in view this scenario and limitations of water spray systems, a
dry type control system would be suitable for such crushers to ensure a
desired level of dust control.
The dry type dust control
system comprises of adequate Enclosure of key locations with hooding
arrangement for extraction of the dust, and arrangement of Cyclone or
Settling Chamber to collect the coarser portion of the dust, and a
Bag-filter house to capture the finer portion of the emission not
captured by Cyclone or Settling Chamber etc. The sufficient capacity of
extraction and pressure drop across the system would be required to be
provided by installing an induced draft fan of sufficient capacity. The
details of the systems component are briefly described below:
● |
Adequate Enclosure and Hooding Arrangement for Key Locations |
● |
Hooding
and Extraction System Arrangement |
● |
Coarse
Dust Control Arrangement as Pre Collector |
● |
Bag
Filter Type Final Dust Collector |
● |
Induced
Draft (ID) Fan |
The dry type system is
suitable for the area where water scarcity is also a big problem (mostly
dry region). The cost is more than the wet type system and reduces dust
upto 90% in the ambient air.
Combination Control System
– Dry & Wet Type
As an alternative to the
expensive dry type control systems in terms of capital investment as
well as annual operating cost, a combination of dry and wet type control
system has also been suggested. In the combination system the dust is
suppressed at some points with water sprays and from some points the
dust is extracted with the help of an induced draft fan and can be
captured in dry type or wet spray chamber type control equipment. Such
combination control systems are commonly used in stone crushers in
developed countries like USA.
This has benefits in terms
of avoiding a coating of dust on the stone products, reduces dust upto
99% in ambient air and at the same time is less expensive than dry type
control system, however it would be more expensive than wet type system.
Conclusions
Based on the above study
in stone crushing industry, it is concluded that, the existing control
measures such as, dust containment enclosures, water spray arrangements
etc., are generally found to be inadequate, due to inadequate
containment, inadequate water quantity, inappropriate spray locations
etc. The environmental management scenario in the
stone crusher sector can be substantially improved through
designing and adopting customized cleaner
production schemes. Adoption of such scheme
would also increase the productivity of units by way of reduced dust
generation, reduced energy consumption, lesser breakdowns leading to
increased plant easy accessibility.
Back to Contents
|