Introduction
In the past few decades, there
have been tremendous efforts put in by the Central and State Governments
of our country to address the issue of rural housing shortage through
various housing schemes like Indira Awas Yojana (IAY), Mukhya Mantri
Gram Awas Yojana (MAY), Indiramma Housing Scheme, etc., for below
poverty line (BPL) families. Though addressing the rural housing
shortage has been a high priority area in the five year plans, the
output of these schemes has not been satisfactory in terms of quality,
numbers, user friendliness, environmental friendliness and cost
effectiveness. As a result, there has been tremendous wastage of
Government funds. Both national as well as local NGOs have put in
immense efforts to promote innovative, eco-friendly and low-cost housing
models in rural areas. It is an ongoing struggle to scale up these
models in an economically viable manner due to lack of awareness about
eco-friendly technologies among the rural population, shortage of
sufficient number of green building material enterprises and its supply
chain and lack of trained masons in eco-friendly construction
technologies.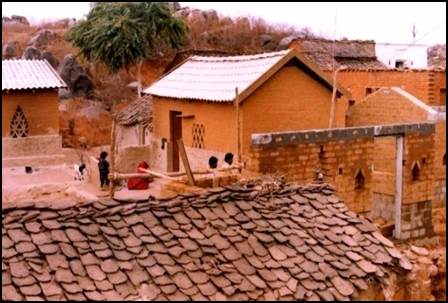
Apart from the rural houses
constructed through various Government housing schemes, a large number
of houses are also constructed in rural areas by the above poverty line
(APL) families with their own monetary savings. Most of these houses are
constructed in an incremental manner as per the savings made in a
particular time period. These sections of the rural population are
concerned about constructing a good quality house (aesthetically and
structurally) in the least possible cost but are not always aware of the
available eco-friendly construction technologies which can satisfy their
needs in a cost-effective manner. They end up spending a huge amount of
money, especially in Reinforced Cement Concrete (RCC) slabs and other
conventional building construction technologies.
From the above analysis, it is
obvious that there is a need to look at the economic perspective of
promoting green lifestyle in terms of eco-friendly building construction
in rural areas.
The Concept of Eco-friendly and Low-cost
Housing
Eco-friendly and low-cost
housing is the concept of building homes using environment-friendly
materials and technologies that will reduce the environmental impact
through construction activities and effective budgeting techniques and
help to reduce the cost of construction. Green and low-cost housing
involves proper management of resources in terms of materials, labour or
money so that the end product has the lowest cost and, at the
same time less environmental impact as a result of the efficiencies that
are practiced during planning and construction of these buildings.
Approach
Following are some of the ways
to reduce the construction cost of eco-friendly rural houses:
·
Efficient use of
locally available building materials
·
Efficient use of
locally available waste by-products from stone quarries or other
industries for the manufacture of building materials like bricks,
concrete blocks, pre cast roofing elements, etc.
·
Use of precast roofing
technologies that do not require any shuttering and take less time for
installation or casting of the roof
·
Efficient structural
design of building elements (roof, walls, vertical and horizontal
structural members) by avoiding wastage of building materials
·
Setting up of small
and medium scale enterprises for production of eco-friendly building
materials using locally available raw materials which also creates
livelihood opportunities for the rural population
·
Creating a proper
supply chain of eco-friendly building materials in rural areas
·
Promoting mass housing
construction activities – scaling up of green housing activities
·
Convergence of
Government-supported housing schemes with NGOs’ approach of eco-friendly
housing construction activities
·
Optimum use of space
in house design
·
Ensuring contribution
by beneficiary families or house owners in terms of sweat equity while
construction of these buildings
·
Training and capacity
building of local masons in green low-cost construction technologies
·
Close monitoring and
supervision while construction of eco houses
Application
For over three decades, the
Development Alternatives (DA) Group has been promoting eco-friendly and
low-cost housing for rural population with the above approach. Following
are some of the green low-cost building construction technologies
promoted by DA.
Rat Trap Bond Masonry Walls
Rat trap bond masonry wall
ensures that there is an economy in the use of bricks, by making a wall
of one brick thickness with fewer bricks rather than a solid English
bond wall. This technology has about 25 per cent overall saving on the
cost of the building when compared to conventional 9" thick masonry wall
construction. The structure has proved its strength for up to three
floors with the support of brick columns. With this technique, there is
reduction in cost of the wall by 25 per cent over the conventional
English bond, where 350 bricks are required per cu m whereas in rat-trap
bond only 280 bricks are required and also the reduced number of joints
reduces the mortar consumption.
Micro Concrete Roofing Tiles for Sloped Roofs
Micro-concrete roofing (MCR)
technology is able to meet the growing demand for high quality roofing.
MCR tiles are a cost-effective and extremely versatile roofing material
and can be used in all applications where a sloping roof is required
using an appropriately designed under-structure (steel and wood under
structure) to make attractive roofs. This technique has been used
extensively in cost-effective housing schemes, workplaces, restaurants
and poultry farms. Micro-concrete roofing tiles are ideally suited to
replace thatch and fired clay tiles in rural areas. A single slope roof
MCR roofing costs Rs 90 psf when compared to conventional RCC roof which
costs around Rs 250 psf.
Plank and Joist Roofing Technology
Plank and Joist is a roofing
system in which precast RCC slabs and planks are supported over pre-cast
RCC beams and joists are placed across the walls. To complete the roof,
concrete is then poured over the gaps between the slabs and the beams,
which then ties all the pre-cast elements together. This technique can
be easily adapted by masons who are familiar with similar techniques of
placing stone slabs over girders to construct roofs in rural areas.
Pre-casting of roof leads to substantial reduction in construction time
and 15 to 20 per cent saving in cost is possible because of the absence
of shuttering and reduction in the quantity of steel.
Conclusion
Eco-friendly construction
material and technologies can only be scaled up if they are marketed
with the tag or value proposition of low cost as well as structurally
sound and aesthetically appealing construction technologies to replace
conventional construction technologies. If successfully scaled up,
eco-friendly and low-cost housing can lead to more people being able to
live in better conditions and can definitely help to improve the quality
of life of rural population.
q
Amol Mangrulkar
amangrulkar@devalt.org