Production of Red Bricks: A
Cleaner Pathway
The
ever-growing population along with rapid industrialisation and
urbanisation process demands millions of new buildings and houses every
year. This has made construction activity as one of the most flourishing
businesses in India and red brick forms the backbone of the construction
sector. India is the second largest producer of soil bricks in the world
after China. It has more than 125,000 registered/unregistered operating
units producing about 250 billion bricks annually (13% of the global
production). India’s red soil brick industry uses conventional firing
techniques, a process which is highly labour intensive and has high
amount of fuel requirement1.
In India, Bull’s Trench Kiln (BTK) is the
most common kiln for firing green soil bricks. Previously it was the
movable chimney variant with two steel chimneys on an oval base. This
technology was modified to the more efficient fixed chimney BTK where
the movable chimney has been replaced by various variants of the
continuous brick firing technologies. Still there are various issues
with the use of the Fixed Chimney BTK technology. The major issue is the
environmental concern. The production of bricks using Fixed Chimney BTK
consumes lots of energy and creates a large environment footprint. The
consumption of coal for the firing of the bricks in FCBTK is very high
and it also results in generation of very high amount of CO2 along with
black carbon and suspended particulate matter (SPM). In some places,
government has banned FCBTK technology which is primarily due to these
environment reasons. So, it is quite important to adopt some new
technologies replacing the existing firing practices.
In this regards, two technologies namely
High Draught Kiln (Zigzag kiln) and Vertical Shaft Brick Kiln (VSBK)
technologies are becoming very popular as they are more energy efficient
and less polluting compared to FCBTK. Between VSBK and Zigzag Kiln, VSBK
is more energy efficient and environmentally cleaner. However, capital
investment for VSBK is relatively higher compared to Zigzag Kiln which
restricts its wide acceptability in medium and large brick enterprises.
Incorporation of cheaper fuels in soil
bricks, such as coal slurry, coal dust, charcoal dust and sawdust can be
used as internal fuels and can help in reducing fuel cost with lower
emission. It has been found that a maximum of 5% (by weight) internal
fuel can be mixed without compromising the brick quality.
Recently TARA has conducted one
demonstration trial in Bihar in the month of June 2019 where waste coal
has been used as internal fuel. The kiln was Zigzag type (natural
draught). Calorific value of the coal dust was 3500 Kcal/kg. The energy
and environment assessment has shown that specific energy
consumption/brick and average emission level have reduced by
approximately 12% and 10% respectively with improved quality of fired
bricks after using internal fuel. As a result, overall fuel cost has
decreased by nearly 30% which is quite significant.
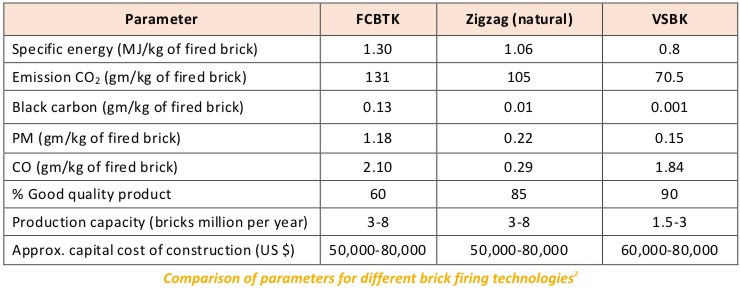
Undoubtedly, internal fuel-based firing
practices are more ecofriendly and energy efficient. In a scientific
manner, this technology can be universally adopted for any types of
brick kilns. As it consumes the waste coal, it also improves the
resource efficiency of the fuel in red brick industries.
■
Endnotes
1. https://www.kenresearch.com/blog/2017/03/soil-brick-making-machine-industry
2. Factsheets about brick kilns in South and South East Asia, A report
by Greentech Knowledge Solution Private Limited, 2014
Palas Kumar Haldar
pkhaldar@devalt.org
Back to Contents
|