Introduction of EcoKiln
Technology in Uganda
Uganda,
a country in East-Central Africa, is bordered to the east by Kenya, to
the north by South Sudan, to the west by the Democratic Republic of
Congo, to the south-west by Rwanda and to the south by Tanzania. The
country has experienced an expansion in urbanisation brought on by
sustained population growth and a period of relative political
stability. This has led to increase in demand for affordable housing and
development of real estate and infrastructure. As a result, the past
twenty years has seen a boom in the building and construction industry
in Uganda, currently growing at a rate of 3.5% annually. Post
liberalisation of the economy in early 1990’s, many foreign and local
investors have selectively entered key sector industries leading to
modernisation of the economy.
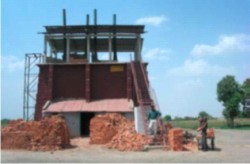
However, brick manufacturing in Uganda has
failed to catch up with the increasing technological advancements and
remains to be an unorganised sector. It is still implementing obsolete
manufacturing processes and technologies that are both energy and
resource extensive and lead to excessive environmental degradation.
Sun-dried bricks are widely used throughout Uganda for low-cost housing,
especially in the rural areas. On the other hand, to support urban
areas, clamp kilns have been widely implemented, utilising firewood as a
primary fuel for firing green bricks. Due to lack of national level
standards and procedures, the resulting bricks are of irregular shape
and size and inferior make, rendering them ineffective for structural
use. Lastly, there is huge wastage of bricks during transportation due
to their poor quality in terms of strength.
According to estimates, the brick industry
in Uganda, by itself, uses around 6 million tonnes of wood on an annual
basis. This enormous consumption of wood on the national level remains
unregulated and has significant adverse impacts resulting in increasing
deforestation thereby affecting biodiversity. In addition, such resource
exploitation leads to high levels of air pollution, soil erosion, forest
degradation, desertification of the landscape and results in reduced
resource availability for other purposes.
It is evident that continuation of the
current scenario would be unsustainable, creating an urgent need to
improve brick production practices in Uganda.
In order to bring about this transformative
change in the country’s brick sector, implementation of a strategic
stepwise approach becomes necessary. As the first step, initiation of
the proof-of-concept phase is proposed, involving construction and
operation of a 2-shaft kiln in Kampala in association with StanBrick
(Uganda-based brick manufacturer). The choice of EcoKiln is based on the
fact that it is the world’s most energy efficient and environment
friendly burnt brick production system and therefore is most suitable to
replace the traditional brick firing system in Uganda i.e. the clamp
kilns.
Introduction of this improved technology
will demonstrate improved quality of bricks, enhanced resource
efficiency, reduced costs compared to equivalent quality and result in
significant energy and environmental benefits. To achieve this, it is
desirable to address the entire brick production system and not adopt a
piece-meal approach to alternative methods i.e. just the firing
technology or the EcoKiln. The entire brick production system needs an
upgrade. In addition, the use of alternative fuels and their efficiency
needs to be studied to ascertain viable options that can potentially
replace firewood.
EcoKiln Technology can be the centre piece
of a technology shift process and drive improvements in related
processes. With improvement in green brick quality and introduction of
internal fuel, properly fired bricks in an EcoKiln would drastically
change the brick industry in Uganda for the better. However, changing an
existing system in the country as a whole, can only be achieved over a
certain time span through consistently learning from experiences in
other countries with similar conditions. ■
Dr. Ankur Sarswat
asarswat@devalt.org
Back to Contents
|